- Guides
The Science Behind Sewer Jetting
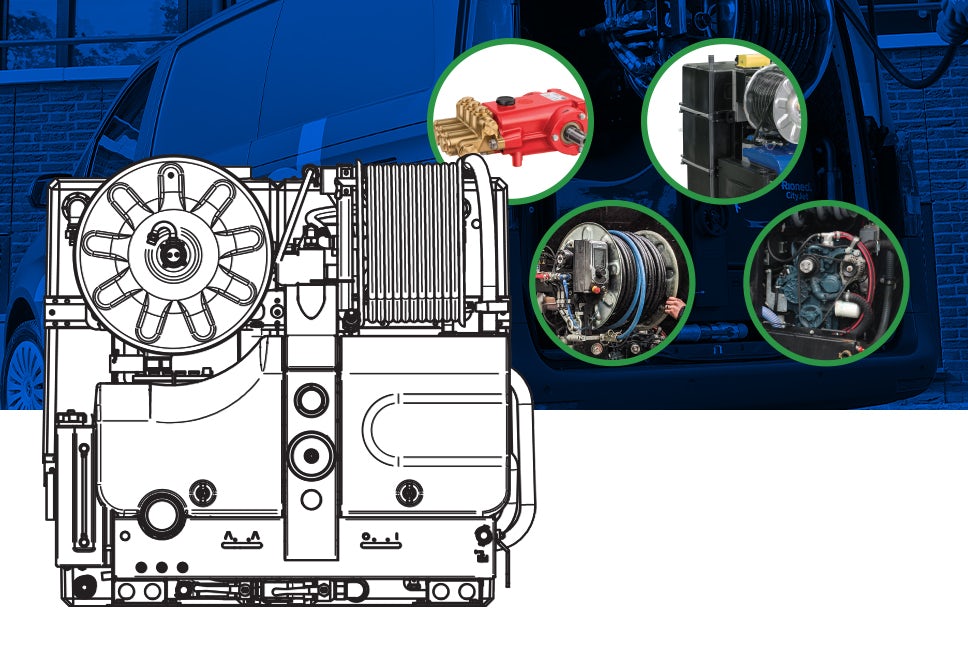
Sewer jetting is a powerful technique that uses fluid acceleration and the power of high-pressure jetting to blast away blockages and clean pipes thoroughly. The water pressure dislodges blockages and removes debris from the pipe walls, preventing future issues, ranging from unpleasant odours and slow drainage to sewage backups and potential health hazards.
How Sewer Jetting Works
Commercial sewer jetting machines typically generate water pressures between 1600 and 4,000 psi (110 bar - 260 bar), and water flow rates of between 2.2 gpm and 16 gpm (10 lpm 72 lpm) based on the type of engine and pump. Individual configurations are used to handle different sizes of drainage pipes and sewers, from small domestic pipework to main sewer lines.
Pressure, measured in PSI or BAR, indicates the force with which water is expelled from the jetter's nozzle. A higher PSI/BAR signifies a greater force propelling the water through the nozzle. This forceful water stream is crucial for effectively breaking up and removing tough blockages, such as tree roots, grease buildup, or solid debris, from sewer pipes.
Flow Rate is the amount of water discharged by the jetter per minute and is denoted as GPM (Gallons Per Minute) or LPM (Litres Per Minute). A higher flow rate means more water passing through the sewer pipe to clear the debris that the pressurised water has dislodged.
The interaction between pressure and flow ensures comprehensive cleaning of the entire drain pipe infrastructure. An understanding of how pressure and flow dynamics operate is imperative for maintaining optimal drain functionality and to mitigate against future obstructions.
How Does a Sewer Jetter create high pressure?
The key components of a water jetter include an engine, a pump, a high-pressure hose, and a nozzle. Here's an overview of how a water jetter works:
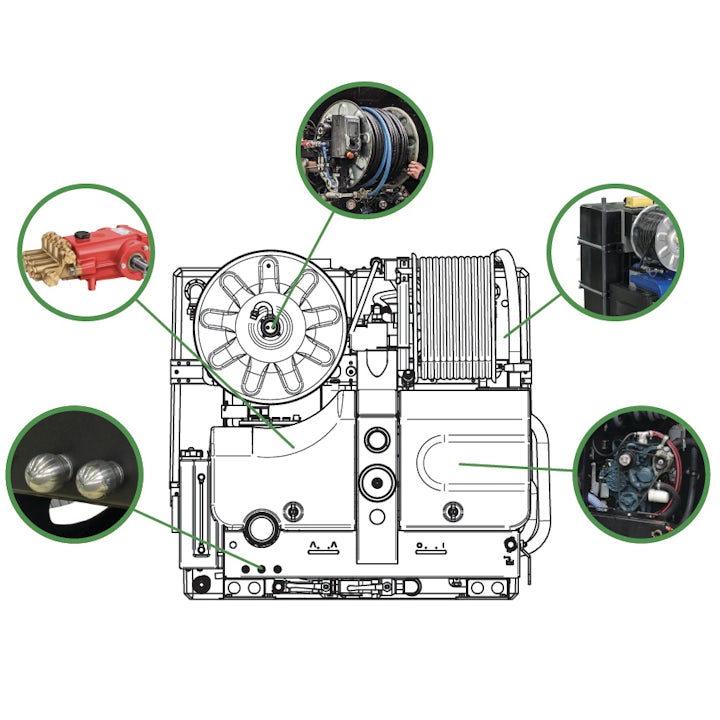
Engines in Sewer Jetting Machines
High-pressure jetting machines in the drainage industry use various types of engines to drive pump systems. The choice of engine depends on the job's specific requirements, the needed mobility, and the availability of power sources. Rioned machines typically run on high-performance diesel, petrol, and electric engines. Power can also be derived from a vehicle's main engine through a power take-off (PTO) system, establishing a direct link between the vehicle's engine and the jetting pump.
In response to the increasing emphasis on emissions reduction, Rioned has proactively developed equipment to comply with environmental standards. The European Stage V norm (equivalent to Tier 4 in the US) specifically regulates emissions from off-road mobile equipment, aiming to improve air quality. These regulatory changes have significantly impacted the industry, especially for diesel engines with an output higher than 19 kW, now required to be Stage V compliant.
The establishment of Low and Ultra-Low Emissions Zones in European cities has also influenced the development and adoption of low-emission power sources. For example, the UrbanJet is equipped with an 18.5 kW engine meeting Stage V standards, while the CityJet features a robust 44 kW diesel engine with a diesel particle filter to adhere to Stage V regulations. Petrol-powered jetters have also gained popularity due to new regulations and advancements in smart engines that combine power and fuel efficiency.
Our all-electric machines utilise highly efficient lithium-ion batteries to drive an electric motor and pump. Offering performance comparable to diesel or petrol machines, these jetters produce zero emissions and significantly reduce noise levels compared to traditional diesel or petrol-powered counterparts. This noise reduction is especially crucial for nighttime operations or when working in residential and congested areas.
The engine provides the necessary energy to drive the pump, which is responsible for pressurising the water.
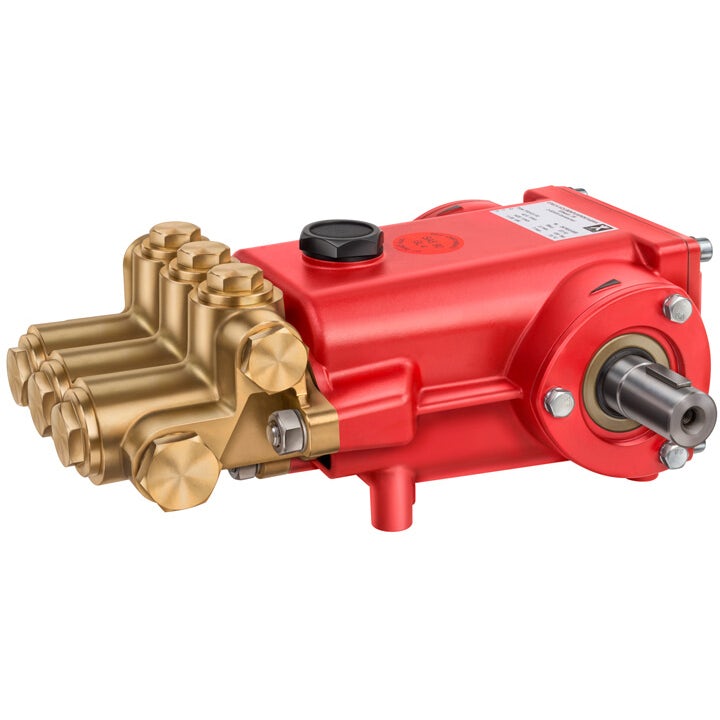
High-Pressure Pumps
The pump is a crucial component that pressurises the water to create the high-pressure jet needed for effective cleaning. There are two main types of pumps used in water jetters:
Triplex Plunger Pumps
A Triplex Plunger Pump is a type of positive displacement pump commonly used in high-pressure water jetting applications. Its operation involves three plungers or pistons that move reciprocally within the pump cylinder. Most Rioned machines use this type of pump due to its ability to deliver a steady and pulsation-free flow of high-pressure water and its durability and efficiency in handling demanding tasks. This reliability is crucial in applications like water jetting, where consistent pressure is necessary for effective cleaning or cutting of materials.
Here's a step-by-step description of the working process:
Intake Stroke: During the intake stroke, the plungers retract, creating a low-pressure zone within the cylinder. This low-pressure zone causes water to be drawn into the cylinder through an inlet valve. The inlet valve opens due to the reduced pressure, allowing water to fill the cylinder.
Compression Stroke: As the plungers continue their movement, they begin to compress the water within the cylinder. The inlet valve closes to prevent water from flowing back, and the compressed water is forced out through an outlet valve.
Outlet Stroke: The outlet valve opens during the outlet stroke, allowing the pressurized water to be expelled from the pump. The three plungers operate in a phased manner, ensuring a continuous and pulsation-free flow of high-pressure water.
Repetition: The entire cycle repeats rapidly, driven by the power source (an electric motor or an internal combustion engine). This repetitive process generates a consistent and high-pressure stream of water, suitable for various industrial cleaning and cutting applications.
Axial Cam Pumps
This type of pump consists of a series of pistons arranged in a circular pattern around an axle or cam. The pistons are typically mounted at an angle to the axis of rotation, allowing them to reciprocate as the cam rotates. While they are more compact and lightweight than triplex pumps they are less robust and are generally used in lower-pressure applications such as pressure washers.
Cam Rotation: The entire assembly rotates, causing the pistons to go through the intake, compression, and outlet strokes sequentially. The continuous rotation of the cam ensures a steady flow of high-pressure water.
Rioned Machine Operation Specifications
Jetting Machine | Engine | PSI (Pressure) | GPM (Flow) | Max Pipe Size |
(Portable Jetter) | Electric (1.8kW / 230V - 50Hz) | 1600 | 2.2 | 100mm |
(Portable Jetter) | Petrol (8 kW / 11hp) | 1900 | 8.8 | 150mm |
(Van-pack Jetter) | Electric (17 kW/h) | 2175 | 13 | 300mm |
(Van-pack Jetter) | Petrol (15 kW / 20 hp) (18 kW / 24 hp) | 2200 | 10 | 300mm |
(Trailer Jetter) | Petrol (15kW /20 hp) | 2200 | 12 | 350mm |
(Van-pack Jetter) | Diesel (18.5 kW / 25 hp) Petrol (23 kW / 30 hp) | 3000 | 10 | 350mm |
(Van-pack Jetter) | Electric (34.2 kWh) | 3000 | 13 | 450mm |
(Van-pack Jetter) | Petrol (42.5 kW / 57 hp) Diesel (33 kW / 44 hp) | 3000 | 16 | 450mm |
(TrailerJetter) | Petrol (42.5 kW / 57 hp) Diesel (33 kW / 44 hp) | 3000 | 16 | 450 mm |
(Van-pack Jetter) | Diesel (33 kW / 44 hp) (49 kW / 65 hp) | 4100 | 18 | 600mm |
How Jetting Machines Work in Operation
The sewer jetter is connected to a water source, which can be a municipal water supply or a dedicated water tank on the jetter itself. The water source supplies the water that the pump pressurises. The pressurised water is then conveyed through a high-pressure hose from the pump to the nozzle. These hoses are reinforced with materials such as steel to withstand the high pressures involved.
Nozzles
The nozzle is the business end of the water jetter. It's attached to the end of the high-pressure hose and is responsible for shaping and directing the high-pressure water jet. Nozzles come in various designs, including rotating nozzles, fixed nozzles, and specialist nozzles for specific cleaning tasks.
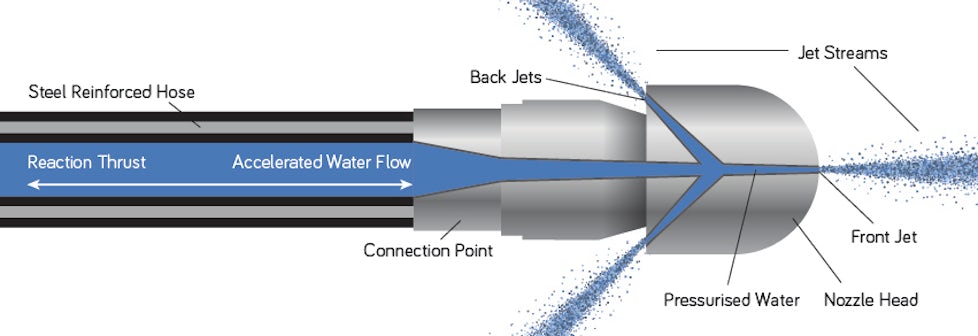
What Are The Forces Involved in Sewer Nozzles?
Jetting nozzles play a pivotal role in dislodging debris, removing blockages, and ensuring the smooth flow of wastewater. The forces involved in this process are rooted in the principles of fluid dynamics and Newton's laws of motion.
1. Fluid Acceleration and Reaction Thrust
At the heart of sewer nozzle operation is the expulsion of pressurised water. As the high-pressure water passes through the nozzle, it undergoes a rapid acceleration. According to Newton's third law of motion, for every action, there is an equal and opposite reaction. In this context, the action is the accelerated flow of water through the nozzle, and the reaction is the equal and opposite force exerted on the nozzle itself.
This reaction force, often referred to as reaction thrust, propels the nozzle forward. The expelled water gains momentum as it exits the nozzle, creating a backward force on the nozzle, resulting in its forward movement. This dynamic is harnessed to navigate and clean pipelines efficiently.
2. Effective Jetting and Fluid Impact
Sewer nozzles are designed with specific configurations to optimise the impact of the water jet. Various nozzle shapes, such as rotating nozzles or those with multiple jets at different angles, are employed to achieve effective cleaning. The force applied to dislodge debris comes not only from the forward movement of the nozzle but also from the focused and pressurised impact of the water on the pipe walls.
The high-velocity water stream can break down and flush away accumulated material, roots, grease, and other obstructions. The forces generated by the water jet are finely tuned to ensure thorough cleaning without causing damage to the pipeline itself.
3. Balancing Forces for Control
Control is key in sewer cleaning operations. The forces generated during operation must be carefully balanced to maintain stability and precision. Engineers consider factors such as water pressure, flow rate, and the design of the nozzle to achieve optimal results. Too much force may risk damage to the pipeline, while too little may result in ineffective cleaning.
The Benefits of Using a Sewer Jetter
Sewer jetting offers a multitude of advantages for drainage professionals:
Effectiveness: Sewer jetting consistently delivers exceptional results, clearing blockages and cleaning pipes thoroughly.
Efficiency: The high-pressure water jet rapidly clears clogs and cleans pipes, reducing overall cleaning time.
Versatility: Sewer jetting can accommodate a wide range of drain cleaning applications, from clearing blockages to maintaining sewer lines.
Safety: Sewer jetting eliminates the need for harsh chemicals or excavation, promoting a safer work environment.
Environmentally Friendly: Sewer jetting utilises water, a natural resource, and avoids the use of harmful chemicals.
Sewer jetting provides drainage professionals with a powerful and effective tool for maintaining healthy and functional sewer systems. By understanding the science behind sewer jetting and its practical applications, drainage professionals can optimise their services and deliver exceptional results for clients.
- Guides